Electronic Parts Related
As we work towards the mobility society of the future, Tokai Kogyo will use our unique technologies to support the development and mass production of electronic components essential for next-generation vehicles, including HVs and EVs.
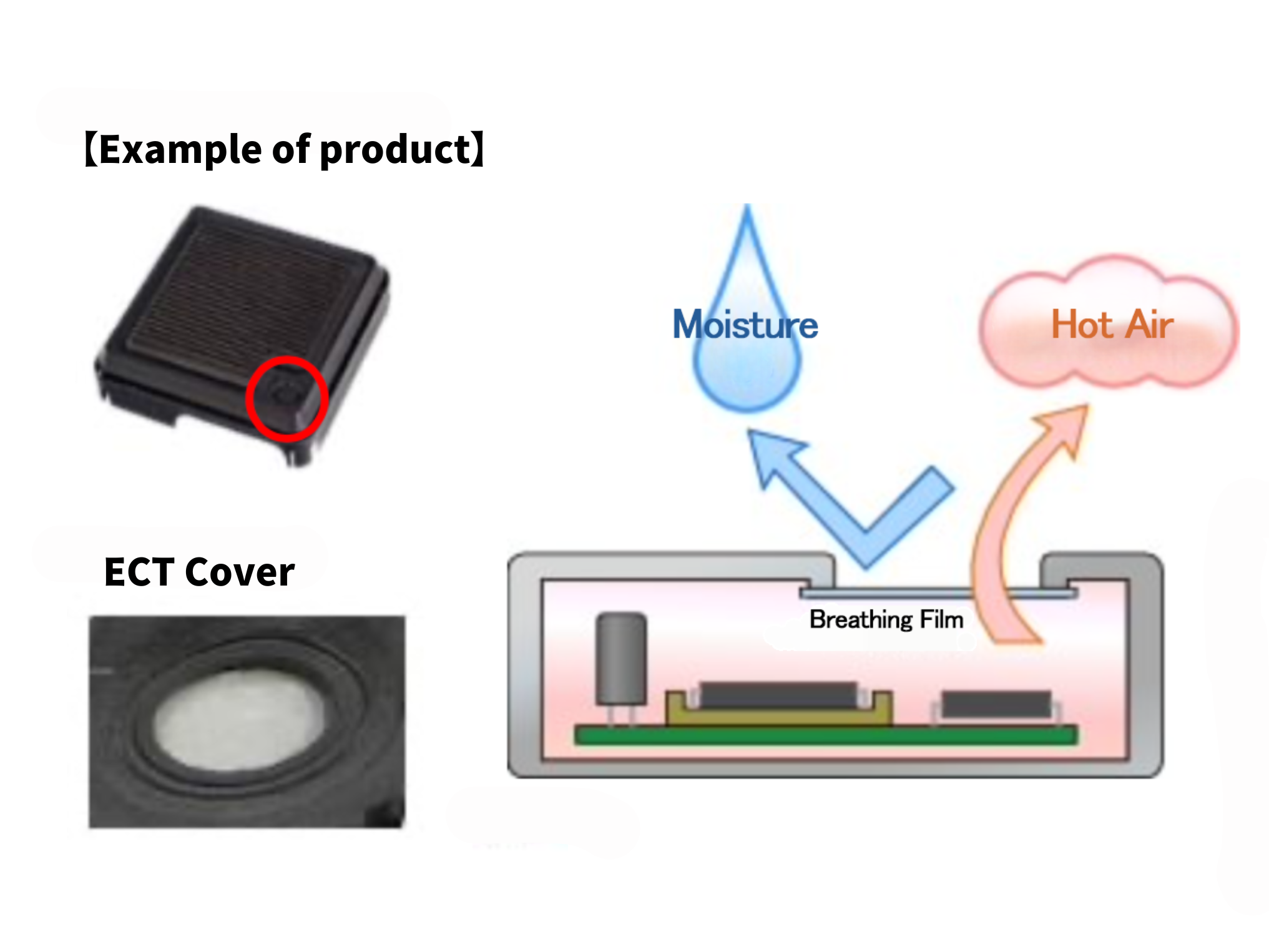
01 Neo Tex Insert Molding
We insert breathable films into the mold and attach the breathable films to plastic products. The breathable film reduces pressure differences caused by heat generation inside the ECU to prevent absorption of moisture during depressurization.
<Merit>
1.This allows elimination of the attachment process for the breathable film.
2.The number of parts can be reduced.
3.The breathable film connectors are easy to guarantee.
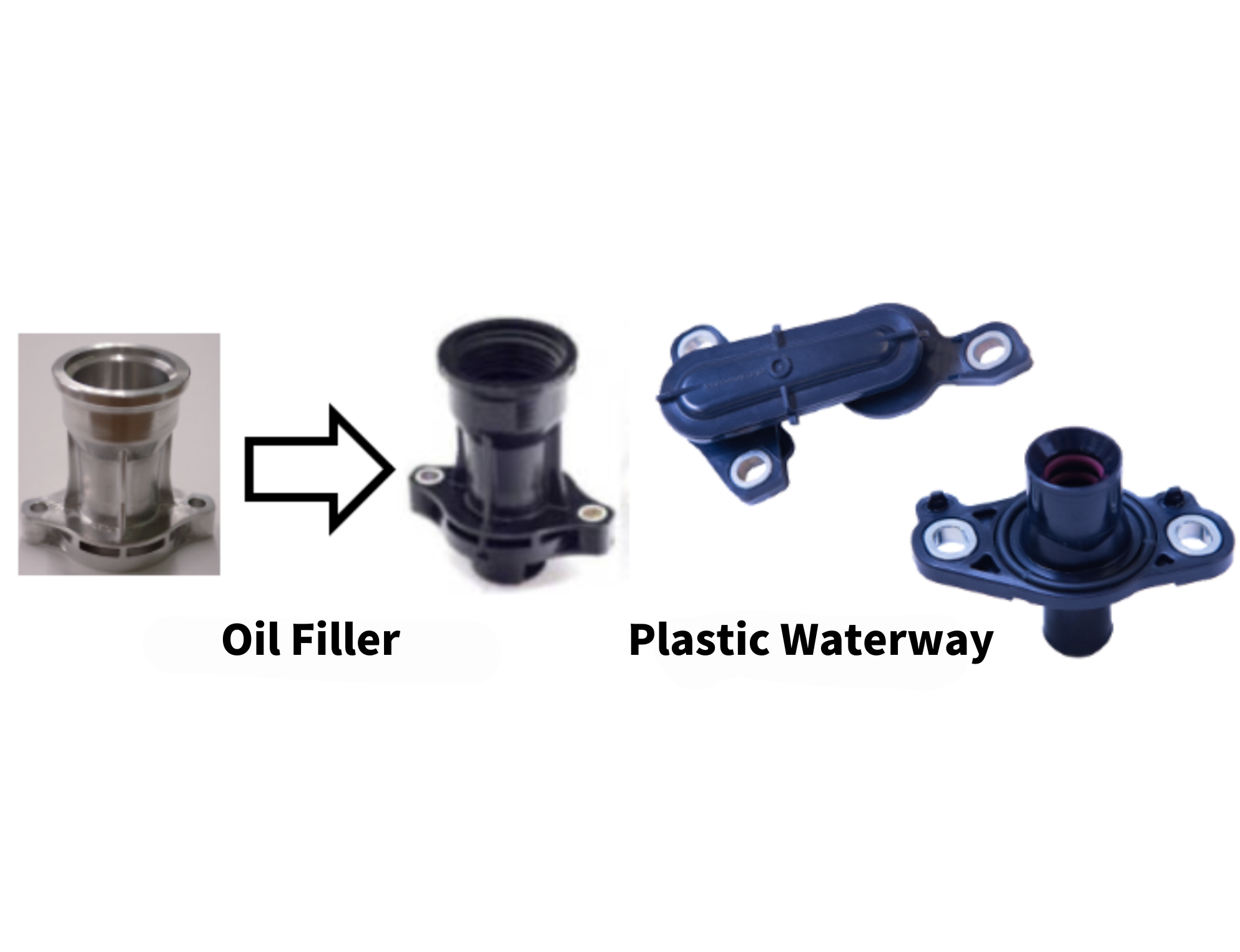
02 From Metal to Resin
By replacing the material from metal with resin, we achieve lightweight, contributing to improved fuel efficiency.
<Merit>
1.That produces improved fuel consumption or electricity costs by reducing weight.
2.Significant cost reductions can be achieved with our unique mold technology.
3.It is getting attention because of its ability to contribute to carbon neutrality.
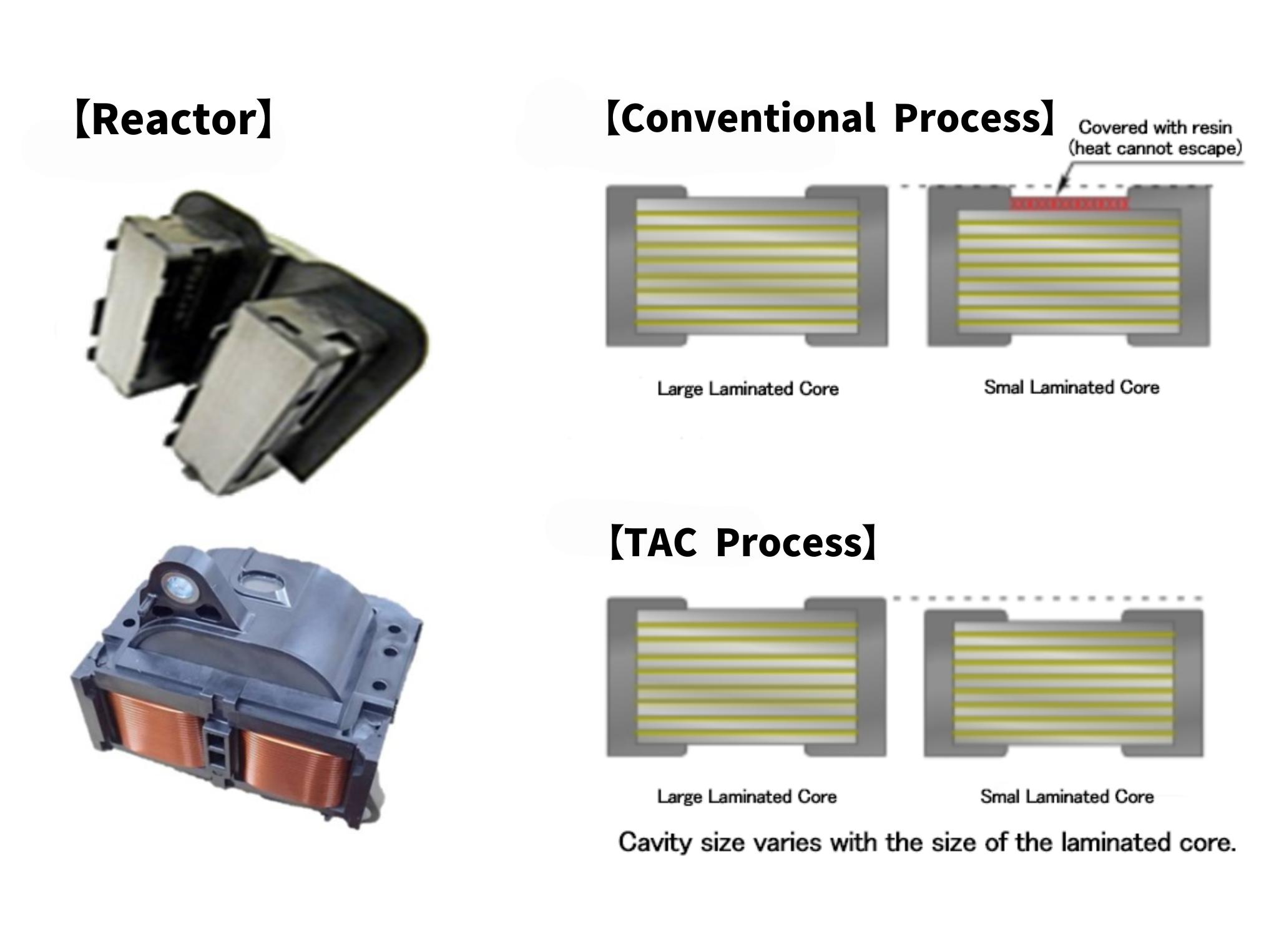
03 TAC Molding Process
The mold cavity size can be adjusted to fit variation in the dimensions of insert parts.
This enables stable production, even when insert parts have large dimensional variation, which is the case with laminated cores or sintering cores.
<Merit>
Even if the size of the insert part changes,
1.Molding can be carried out without finishing.
2.Stable production is possible without damaging the mold.
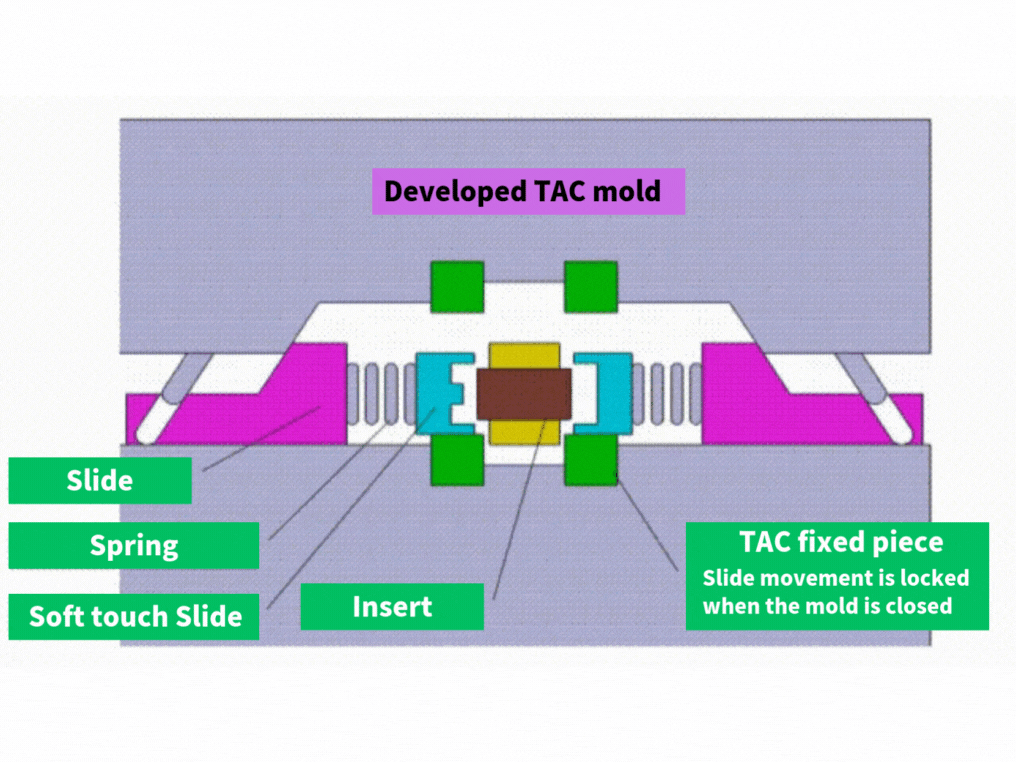
This is a dream-like mold with a mechanism that allows the mold to adjust even if the size of insert parts varies widely. By locking the light blue slide with the green piece, the insert molding is not affected by withstanding the injection pressure of the resin. The soft-touch capability of the inserts also enables us to mold resin even if you need to make soft inserts.